
Partec
- INDIRIZZO: Via Campignano, 9
- LOCALITA': PARRE - (BG) - ITALIA
- TELEFONO: +39 035705800
- FAX: +39 035705820
- WEBSITE: www.partec.it

ABOUT US:
Rapid prototyping is a group of innovative technologies that permit the realization of some complex pieces in a brief period of time, from the receipt of the 3D CAD models.
Partec was born in 1999 as a service completely dedicated to rapid prototyping, with two implants of stereolithography and one implant of vacuum casting. In 2001 Partec add the sintering technology and in 2004 the first implant of Metal Part Casting for the fusion of low-melting alloy has been installed.
Today Partec realizes prototypes through these technologies:
- Stereolithography (SLA) – n°3 implants
- Select laser sintering (SLS) – n°2 implants
- Vacuum Casting – n°2 implants
- Metal Part Casting – n°2 implants
SERVICE:
Stereolithography (SLA) is the most precise of rapid prototyping technologies; layer upon layer the resin solidified by a laser forms the prototype inside the machine. By the stereolithography the piece is ready in only three days.

Stereolithography process

Pieces realized by stereolithography
Sintering of nylon permit the realization of particulars with good dimensional qualities and excellent mechanical characteristics. The process can be used for evaluating the functionality of the product but also for the creation of pre-series, considering the extreme hardness of the working surface and the cheapness.
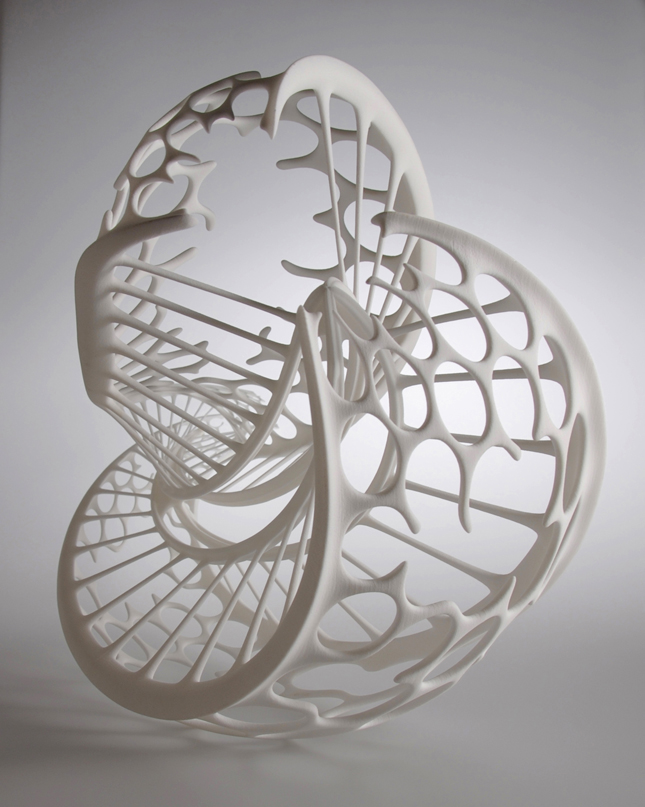
Sculpture realized by sintering of nylon
Vacuum Casting is the best way to produce in small series and at profitable costs. The process starts from a SLA piece that will be used as a master for the realization of the silicon mould; then the resin will be casting inside the mould and will form the final piece. By this method it is possible to realize co-moulded particulars, combining different materials.
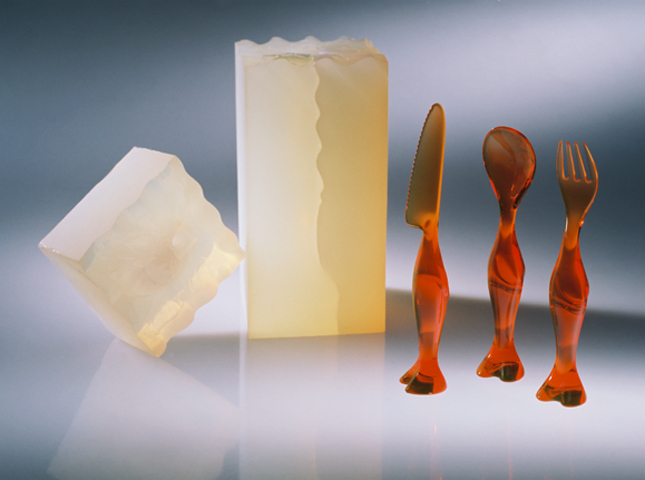
Examples

.jpg)
Example of a co-molded piece
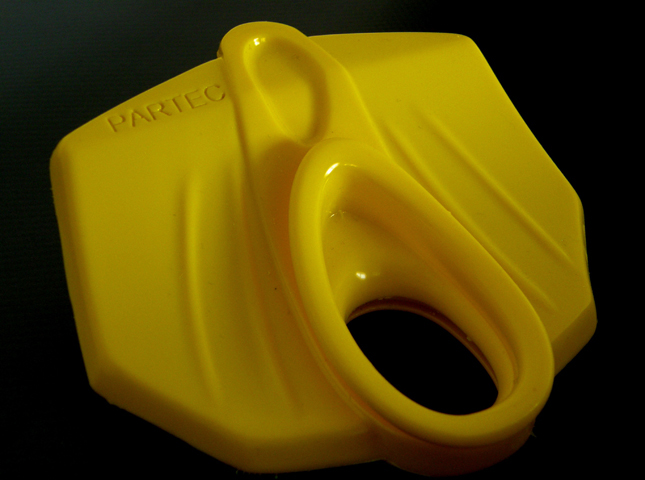
.jpg)
Replica formata da due diversi materiali
Metal Part Casting permit the realization of Aluminium, Brass or Zama pieces, with complex geometries and with a good precision level. Depending on the characteristics that the pieces should have, the master will be in wax or polystyrene. The first permits high production and best surface finish, the second is suggested for complex geometries or thin depth.
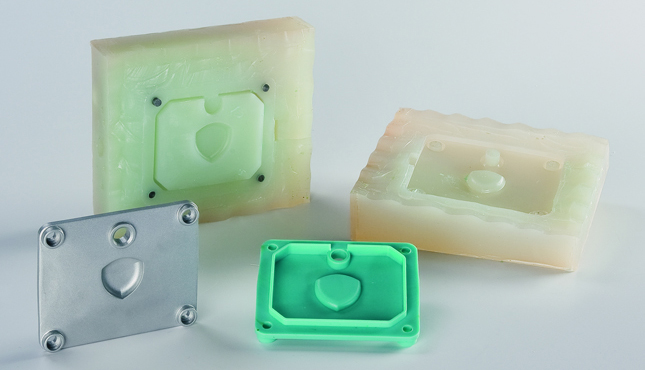
Brass piece obtained from a wax pattern
.jpg)
Aluminium piece obtained from a polystyrene pattern